3D Laser Scanning – Historical Aspect & Development
The inception of 3D laser scanning dates back to the 1960s, when laser technology was introduced for the first time. In the 1980s, LIDAR systems started to be used for aerial mapping. Then, the technique of terrestrial laser scanning became popular in the 1990s for ground-based 3D scanning. In the 2000s, the integration between laser scanning with GPS and IMUs was observed for georeferencing.
This technology began to be used in different industries during the 2010s. Since then, the accessibility and applications of 3D laser scanning have expanded due to its miniaturisation and cost reduction. Now, it is being used in various fields, including the construction industry, cultural heritage preservation, and manufacturing industry.
This article will help you understand 3D laser scanning, its importance, and the equipment and elements used during this process. You can also learn about this method’s principles, techniques, procedure and applications in different fields. Moreover, this guide also includes information about the advantages and limitations of the 3D laser scanning technique.
3D Laser Scanning
3D laser scanning is an advanced technique involving laser beams for accurately measuring distances to surfaces and creating different environments, landscapes, and objects with detailed 3D representation. It is done by targeting laser beams towards a particular object or surface and measuring the time in which laser pulses bounce back. The wavelength of light changes when it bounces back, and this variation is measured by the scanner.
Then, the measured time is combined with the angular information, enabling the scanner to calculate the distance and orientation of all the points on the surfaces of objects. During this process, multiple laser beams are emitted from various angles. This helps capture the dense set of 3D coordinates, which creates a point-cloud representation of the targeted objects. It is one of the most accurate, quick, and safe solutions to gain three-dimensional on-site data measurements, which makes it ideal for use in the design and project management phases.
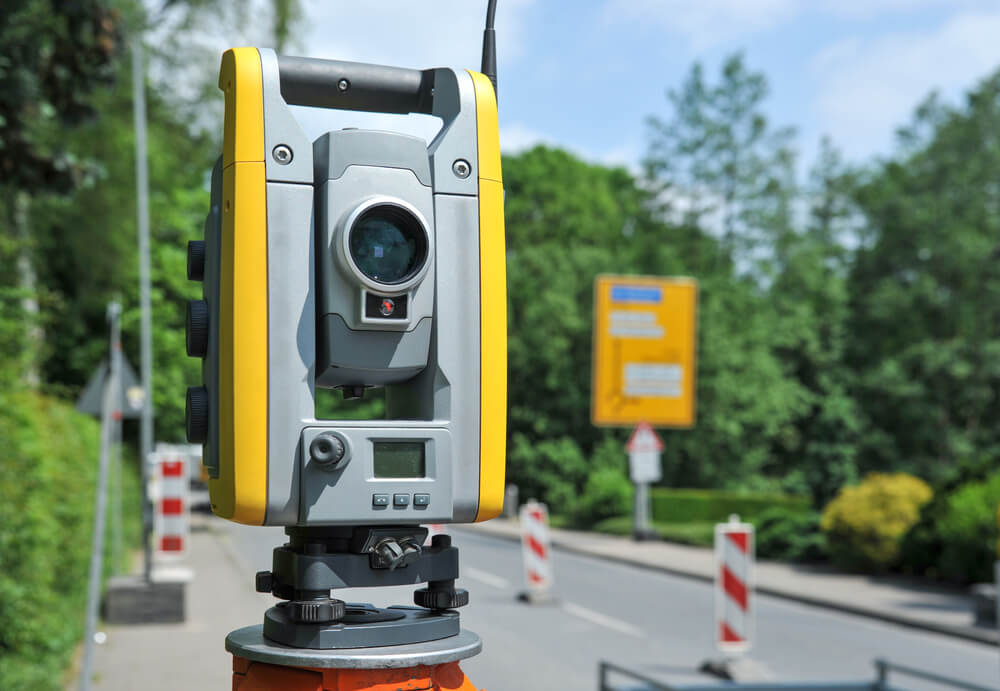
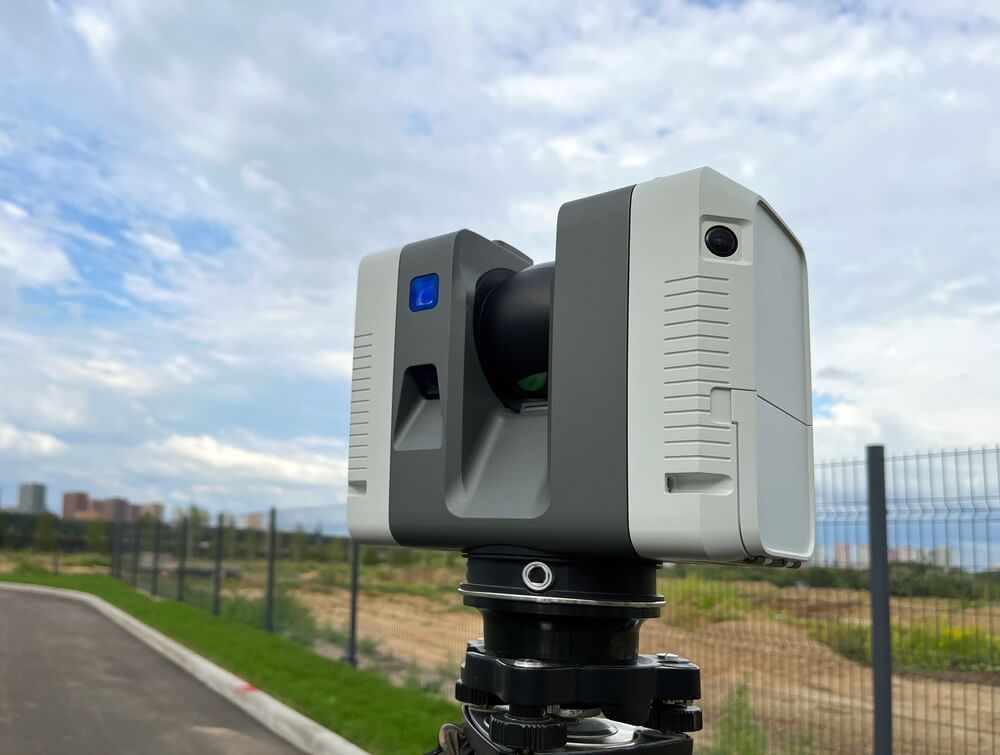
Importance of 3D Laser Scans
3D laser scans of a building yield valuable information related to:
- Profiles
- Sections
- Elevations
- Floor Plans
- 3D Meshes or Models
- Raw Point-Cloud Data
This information is essential for:
- Space Planning
- Clash Detection
- Facility Management
- Historical Preservation
- As-Built Documentation
- Architectural & Engineering Design
3D laser scans can also provide accurate and detailed information about a building’s condition and geometry. These details help stakeholders make informed decisions about construction, renovations, and facility management projects.
Equipment & Elements Used for 3D Laser Scanning
The following are the equipment and elements used during 3D laser scanning:
- Tripod: It is utilised for mounting the laser scanner and stabilising it while scanning.
- Processing Software: It helps in the conversion of raw point cloud data into a 3D model.
- Laser Scanner: It emits the laser light’s beam for measuring the object distance in its view field.
- Data Recorder: This device works for storing the raw point cloud data that is captured by the laser scanner.
- Target: This is the reflecting object positioned around the scanning area to assist the laser scanner in registering and aligning the scans.
- Other Accessories: Some other accessories can also enhance the system’s capabilities, such as a high-resolution camera that captures images of the area being scanned. A GPS receiver can be utilised to accurately place the 3D model in real-world coordinates for georeferencing. A scanner controller can also help the operator control the laser scanner and scan data’s view in real-time.
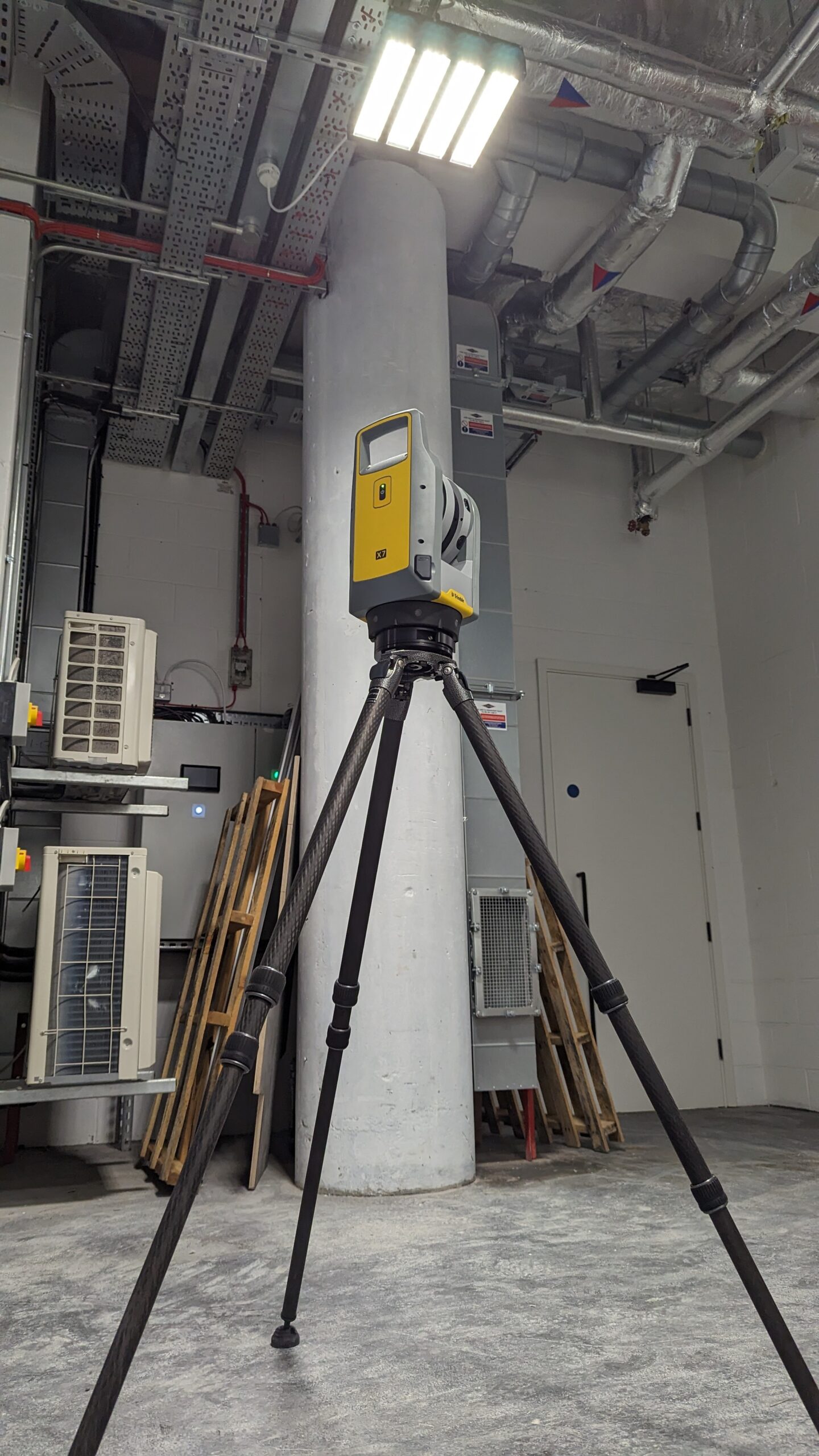
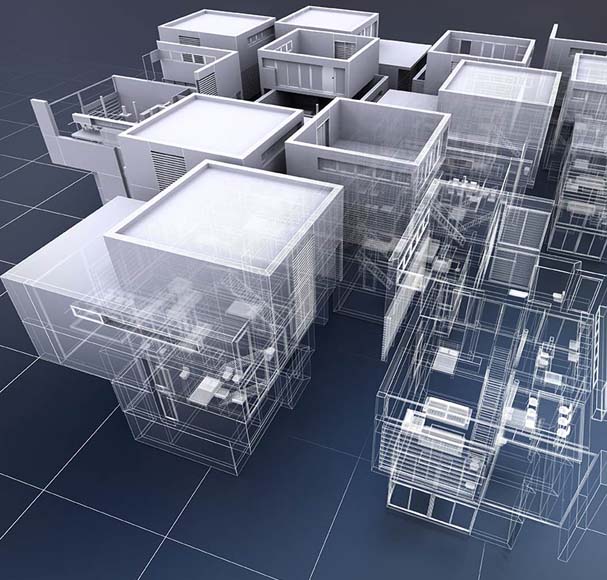
Principles of 3D Laser Scanning
3D laser scanning is also called TLS (Terrestrial Laser Scanning) or LIDAR. This technique is used for capturing the three-dimensional shape of an object with the help of laser light, contributing to the creation of detailed 3D models. The two major principles of this technique are:
- TOF (Time of Flight): It refers to the measurement of time a laser pulse takes for travelling from the scanner to the object and then return. The speed of light is used to measure the object distance.
- Phase-Shift Scanning: It helps measure the phase difference between the emitted and the reflected laser beam. Then, the principle of interferometry is used to calculate the distance to the object.
Techniques of 3D Laser Scanning
Different techniques are used in 3D laser scanning to obtain results with a high level of accuracy and precision. These techniques include:
- Intensity-Based 3D Reconstruction: It is a technique in which reflected beam’s intensity is used for classifying different types of surfaces and identifying the boundaries of various objects.
- Multi-Scan Registration: In this technique, multiple scans of the same targeted object are combined for creating a detailed and precise 3D model.
- Triangulation: In this technique, the distance to the objects is calculated using the scanner’s geometry, targeted object, and reflected beam.
The Procedure for 3D Laser Scanning
To enhance the accuracy of results obtained after 3D laser scanning, the following steps should be followed:
- Define the objective and scope of the project for outlining the 3D laser scanning’s purpose the specific information needed.
- Assess the persisting conditions at the project site, such as its layout, obstacles, and potential safety hazards.
- Get the required approvals and permits to access the site you need to scan.
- Set up all the equipment, such as the laser scanner, tripod, etc., ensuring the scanner is properly aligned and levelled.
- Place the targeted objects at strategic locations for scan registration and alignment.
- Calibrate the laser scanner based on the manufacturer’s instructions to ensure optimal accuracy.
- Plan the locations to be scanned for covering the targeted area completely.
- Overlap the adjacent scans for ensuring seamless integration and reducing data gaps.
- Use consistent scanning settings and parameters throughout the project for consistent quality data.
- Pre-process the point cloud data by filtering out noise and outliers and classifying the points into pertinent categories.
- Use targets or other reference points to align the individual scans for the creation of a unified 3D model.
- Start post-processing the 3D model by smoothing out the surfaces, filling in the gaps, and enhancing the details to get a refined representation.
- A comparison of 3D models with the dimensions or reference data will be conducted to verify their accuracy.
- Check the date completeness for ensuring that the 3D models have captured all relevant details and features of the scanned area.
- Identify and resolve the data errors and inconsistencies in the 3D model.
- Store the data after organising it by implementing a structured data management system.
- Choose a suitable file format which is suitable to use with various kinds of applications and software.
- Undertake secure methods to share and transfer 3D models and all the relevant data.
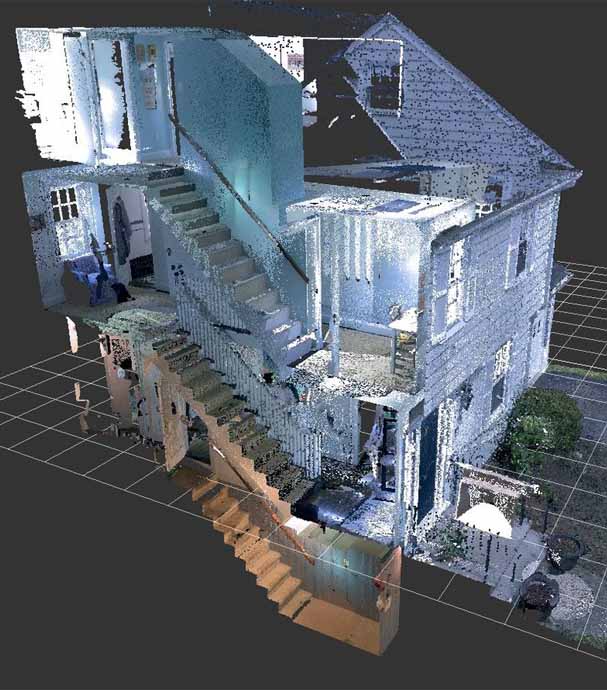
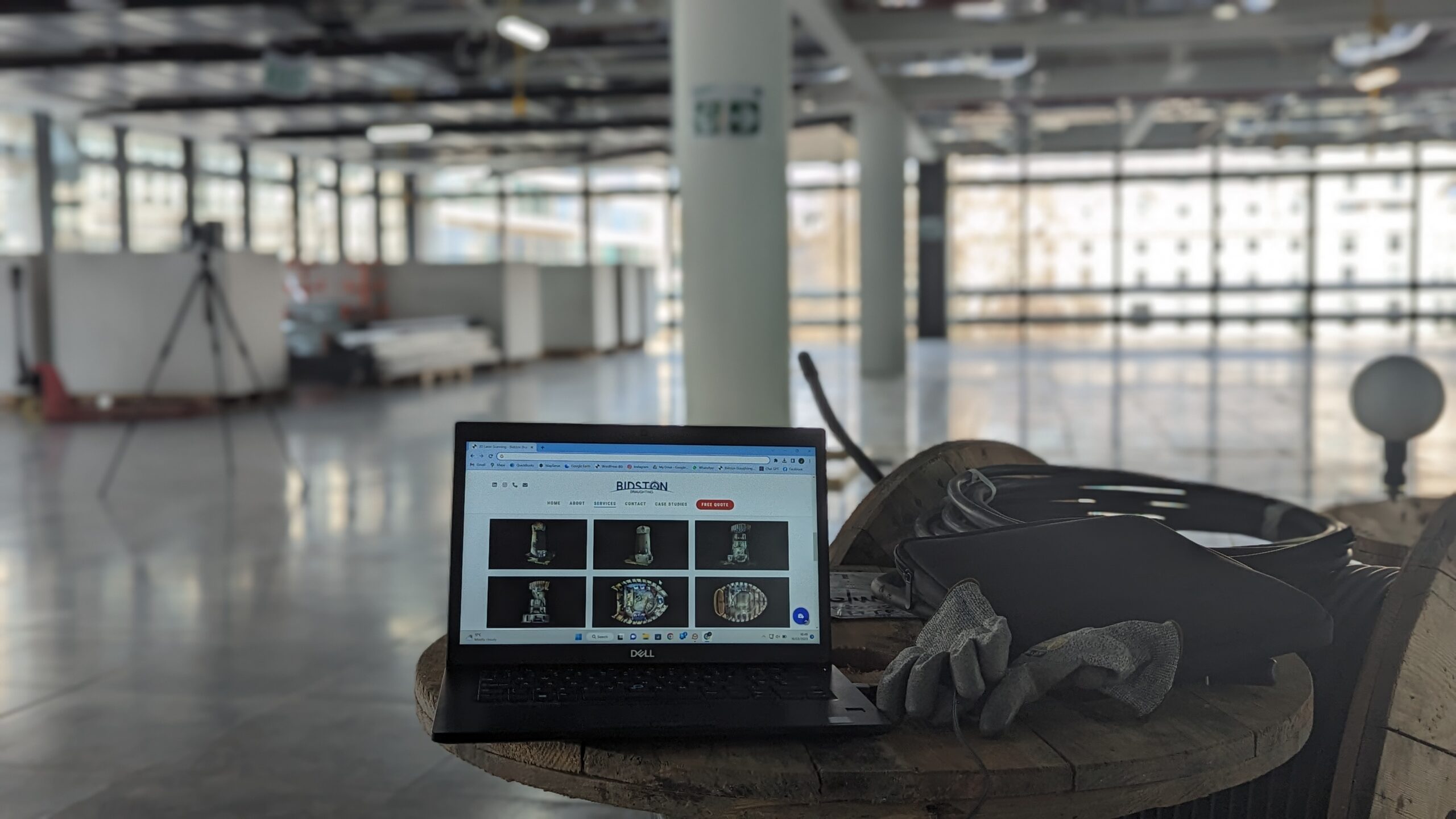
Applications of 3D Laser Scanning in Different Fields
Being a versatile technique, 3D laser scanning has different applications in various fields:
- AEC (Architecture, Engineering & Construction): This technique is undertaken for creating as-built models of different types of buildings and structures, planning and designing new projects, and monitoring the progress of any construction project.
- Archaeology & Cultural Heritage: This method helps in creating detailed models of archaeological sites and artefacts, documenting and preserving cultural heritage, and generating virtual reconstructions of ancient structures.
- Autonomous Vehicles & Robotics: This technique helps autonomous vehicles perceive their surroundings and detect obstacles. Moreover, it is utilised in robotics for guiding robots in different tasks, including object manipulation and navigation.
- Forestry & Environmental Monitoring: The 3D laser scanning technique is utilised for mapping and monitoring forests, assessing tree health, and measuring land cover changes.
- Manufacturing & Quality Control: 3D laser scanning is used for inspecting manufactured parts for defects, measuring complex shapes, and creating digital twins of products.
Advantages of 3D Laser Scanning
3D laser scanning is extensively being used across several industries as this technique helps in capturing accurate and detailed 3D data. The following are some other advantages of 3D laser scanning:
- It helps get precise measurements for various construction, engineering, and product manufacturing applications.
- This technique helps rapidly collect a large amount of data for high-rise buildings, reducing potential risks and improving the safety of field staff.
- It enhances the site analysis and planning by providing a detailed representation of existing site conditions, including different structures, topography, and other utilities.
- This method helps in creating detailed digital records of data crucial data for different buildings, landscapes, and objects and proves to be helpful in preserving the historical archives.
- This technique accurately represents various objects, helping engineers and planners make informed decisions regarding foundation design, grading, and site layout.
- The data obtained after 3D laser scanning is beneficial for creating high-value visualisations that help in designing, analysing, and communicating while constructing complex spaces and structures.
- It is a noninvasive, noncontact technology that eliminates the need for physical contact with the environment or object being scanned. This makes it ideal for scanning fragile, hazardous, and restricted-access areas.
- The 3D laser scanning method can be used with BIM (Building Information Modelling), which proves to be extremely advantageous for identifying clashes between different design plans and existing structures, reducing errors and associated costs in the construction phase.
Limitations of 3D Laser Scanning
3D laser scanning has some limitations, such as it only helps in capturing the line of sight, and x-ray vision is required to record the surface below. This technique is unsuitable for moving objects and can only capture the dimensions of objects that do not change their positions. The water drops can obscure the lens during inclement weather, which causes the laser to start deflecting the light ray instead of bouncing it back, which affects the format of recording dimensions.